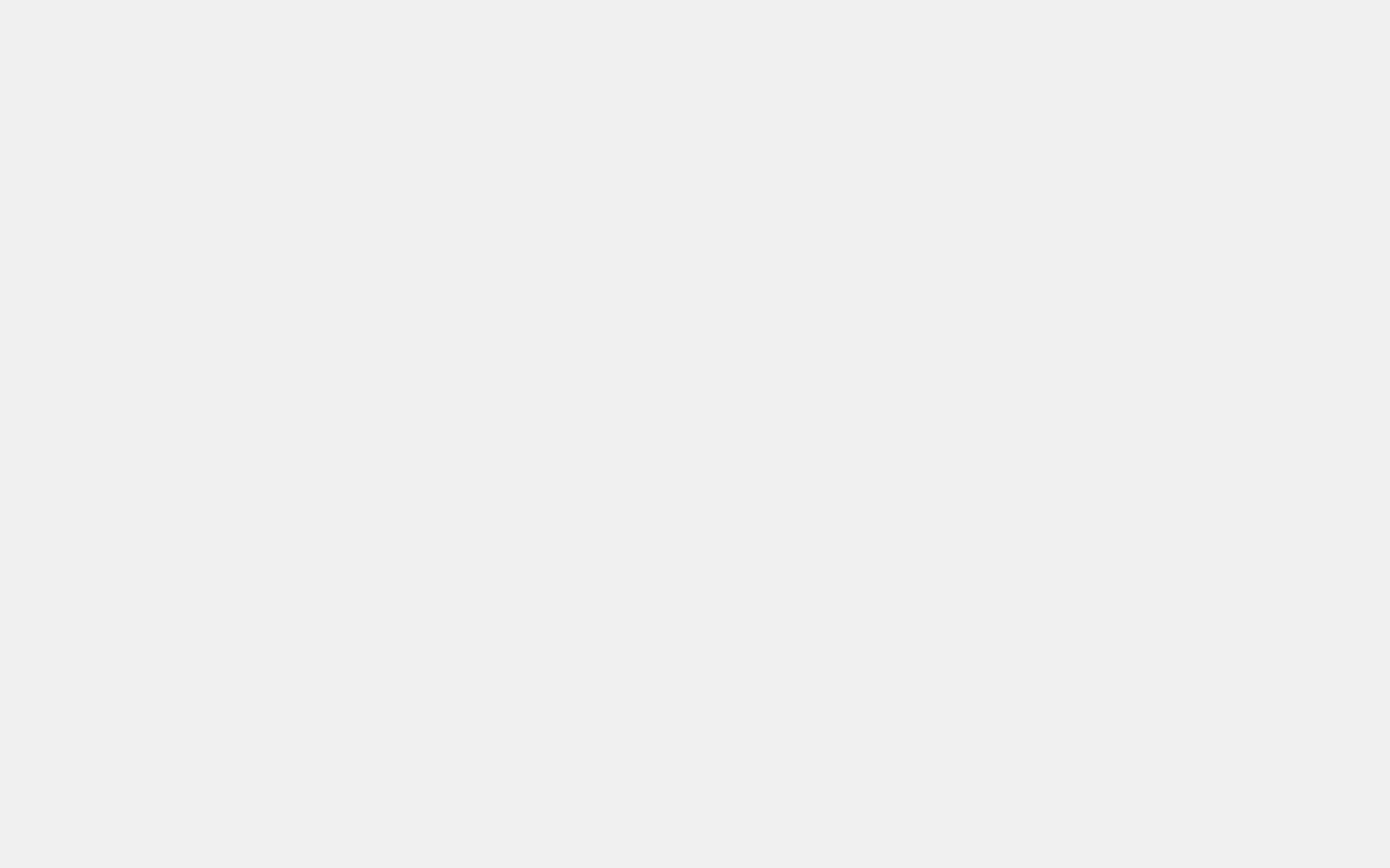
A Sensonetics Mold Cavity pressure transducer uses the same Silicon-on-Sapphire sensing diaphragm that has proven itself in plastic melt and extrusion applications. The sapphire sensing diaphragm is manufactured from a single-crystal aluminum oxide that is the hardest of the metal oxide crystals and is chemically inert. This material known as silicon on sapphire is ideally suited to the mold cavity transducer applications. Sapphire has a modulus of elasticity 30% higher than stainless steel and sapphire is five times more abrasion resistant than tungsten carbide. In fact, the only material that can scratch it is a diamond. The high modulus of elasticity combined with the high gauge factor of the piezoresistive strain gauges results in virtually infinite fatigue (cycle) life. Single-crystal piezoresistive strain gauges are epitaxially grown on the sapphire force collection diaphragm, forming a homogeneous, single-crystal, radiation hardened structure. It can be exposed directly to process media and can withstand continuous operating temperatures to 750°F. An optional RTD is available, providing excellent temperature measurement of the mold isolated from the transducer mounting well.
MOLD CAVITY PRESSURE AND TEMPERATURE
Pressure and temperature are the two most important measurable process variables in the molding process. The use of a mold cavity pressure transducer assures complete mold fill-out when placed strategically in key mold cavity positions. Until now, good measurement tools were not available due to fatigue, lack of durability, and slow response time.
Sensonetics Silicon-on-Sapphire mold cavity pressure transducers provide direct pressure measurement with a faster response time. The sapphire diaphragm has infinite fatigue (cycle) life and will not wear out in abrasive melt applications. The piezoresistive strain gauge allows dynamic as well as steady state pressures to be accurately measured without signal decay. The optional on-diaphragm temperature sensor provides cavity temperature information at the surface of the melt. Both of these parameters are especially important in thermoset molding applications where maximum pressure and temperature occur during the plastication process of the mold.